※記事文章内に記載の登壇者の所属、役職などはウェビナー開催時のものです
プログラム1「サーキュラーエコノミーの現状と日立の取り組み」
プログラム2「サーキュラーエコノミーがめざす社会と経済」
プログラム3 パネルディスカッション「サステナブルな製品開発への挑戦」
Commitment for Disposing 廃棄に対する責任感
助口:
ここからは、サーキュラーエコノミーに関する具体的な研究やデザインの取り組みについて議論を深めます。まずは自己紹介からお願いします。
木田:
ビジョン戦略本部では、魅力ある価値創出に向けた取り組みとして、将来、社会や生活者に起こりうる価値観の変化をきざしとして捉え、そこからバックキャストして新たな価値を提供、創出するビジョン駆動型の商品開発を推進しています。
野村:
家電のデザインを主に担当し、製品の造形だけではなくCMF※という色や素材や仕上げなどの専門チームを取りまとめています。特に再生材活用をCMFの視点から推進しており、先日グッドデザイン賞を受賞した再生プラスチックを活用した掃除機について話したいと思います。
※CMF…モノの表面を構成する三つの要素 Color、Material、Finishのこと
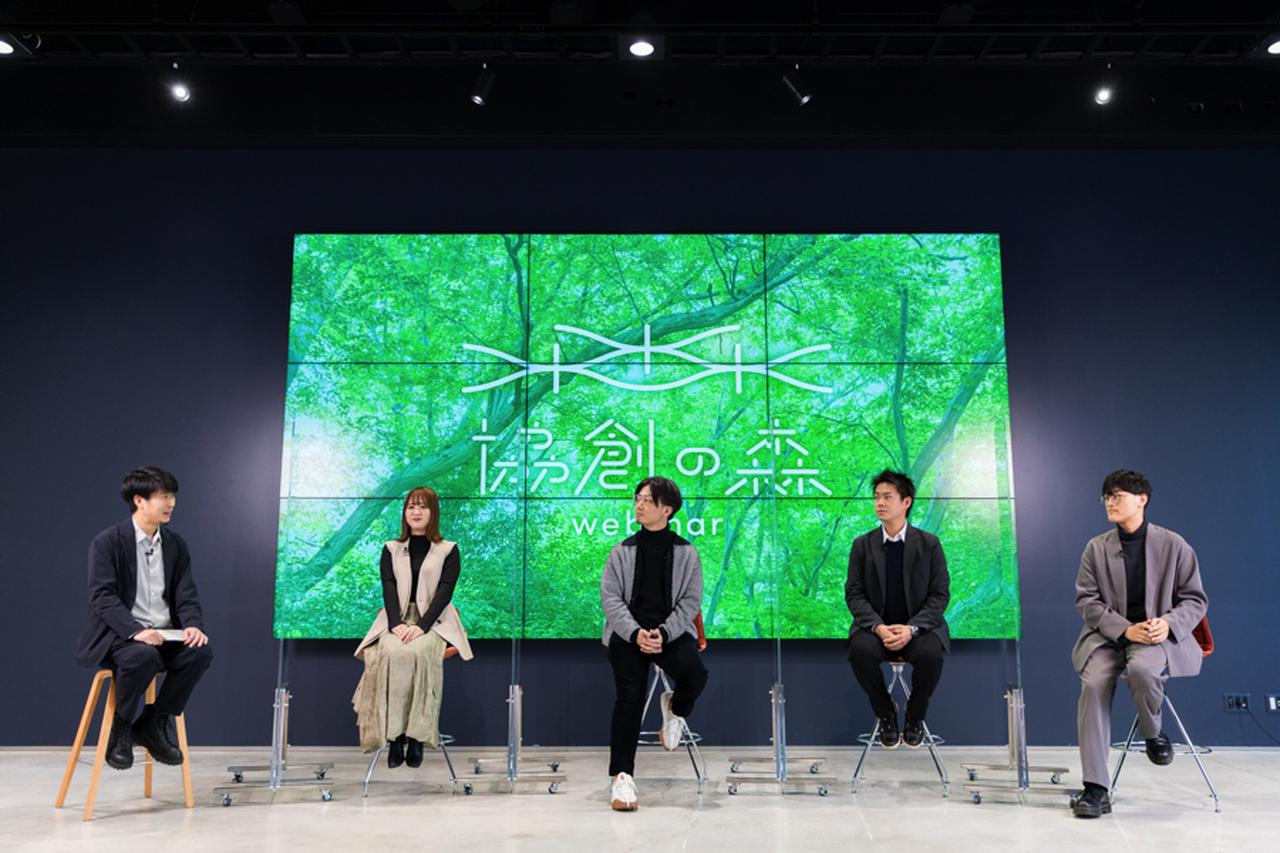
パネルディスカッションで意見を交わした(左から)助口、木田、野村、栗城、八木
栗城:
掃除機の中でも主に国内向けのコードレススティッククリーナーを担当しています。直近では、いま野村さんからお話があった再生プラスチックを活用した掃除機を設計側から担当しました。
八木:
私はプログラム1、2で登壇した谷口さんと同じサーキュラーインダストリー研究部で、製造現場のナレッジとセンサーデータを活用して工場の製造品質や生産性を向上するデジタル技術の開発、再生プラスチックを使いこなす技術の開発など、製造プロセス×デジタルにまつわる研究に取り組んでいます。開発技術がサーキュラーエコノミーの実現をドライブする上でどう役立つことができるのか、日々ワクワクしながら研究しています。
助口:
早速ですが、それぞれの取り組みを順番にお聞きかせください。
木田:
私は個々のきざしをよりリアルなものに感じてもらって社内で将来の製品やサービスのヒントにしたり、未来志向の気づきが生まれるようにブランドメッセージやきざしに関するコンテンツを発信したりしています。
助口:
今いろいろなきざしが出ていますが、この中でサーキュラーエコノミーに関するものや環境意識みたいなものもありますか。
木田:
例えば、Commitment for Disposing 廃棄に対する責任感があります。
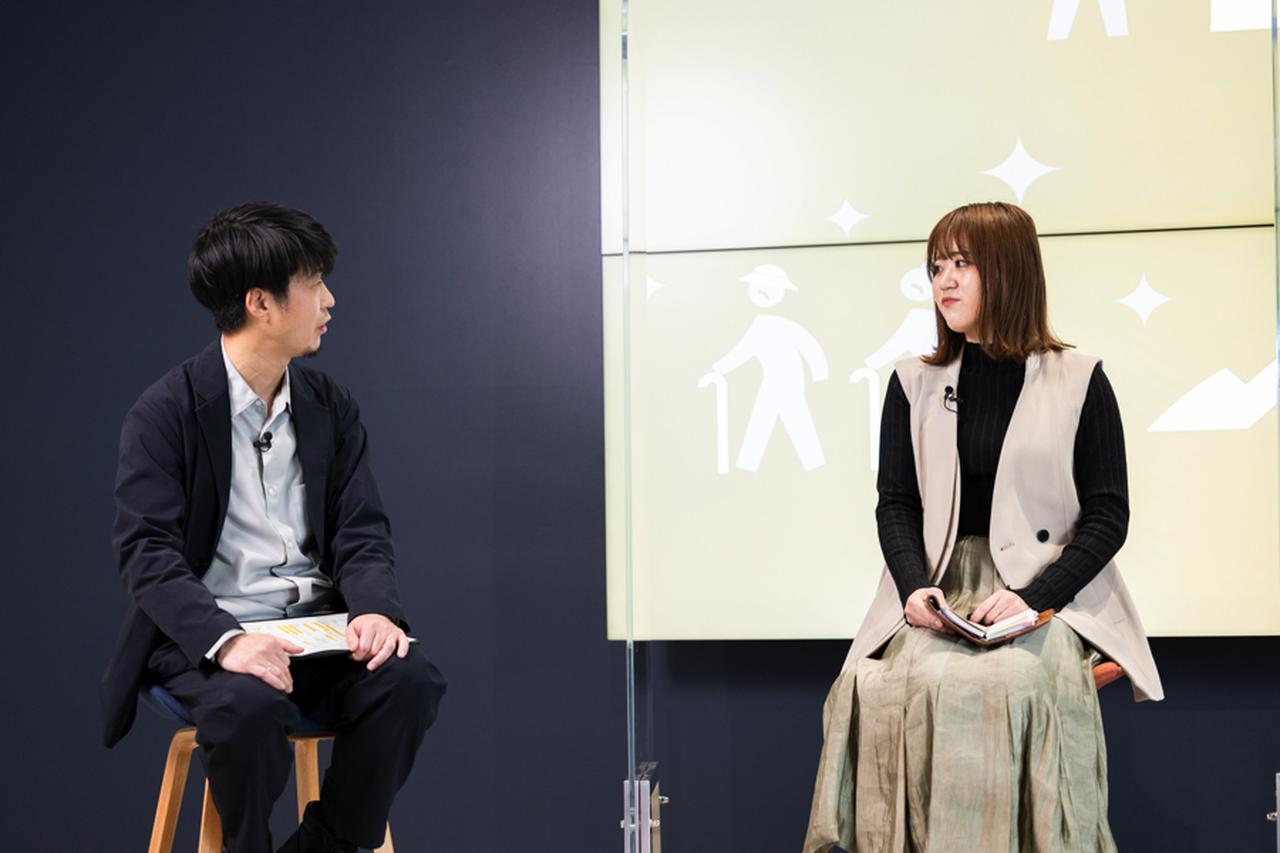
パネルディスカッションは、Commitment for Disposingの事例紹介から始まった
今の時代、再利用や再生可能であることが常識になりつつありますが、その上でできるだけ長く使う、そして捨てる時でも心地よく捨てられるように環境に配慮した材料で作られた商品の普及を加速させるというきざしがCommitment for Disposingです。他にも Criteria for Eco-Fabric 服選びがエゴからエコへ というものがあります。生活者は、製品がエコ素材で作られているかどうか、製造元の企業がエシカルを意識されているかを基準として何を買うかを判断するようになるというきざしです。
私はこういうきざしが実際に起こり始めていることを体現している方々に話を聞き、インタビュー記事を社内に発信しています。
助口:
面白そうですね。インタビューの中でも特に印象に残っていることを教えてください。
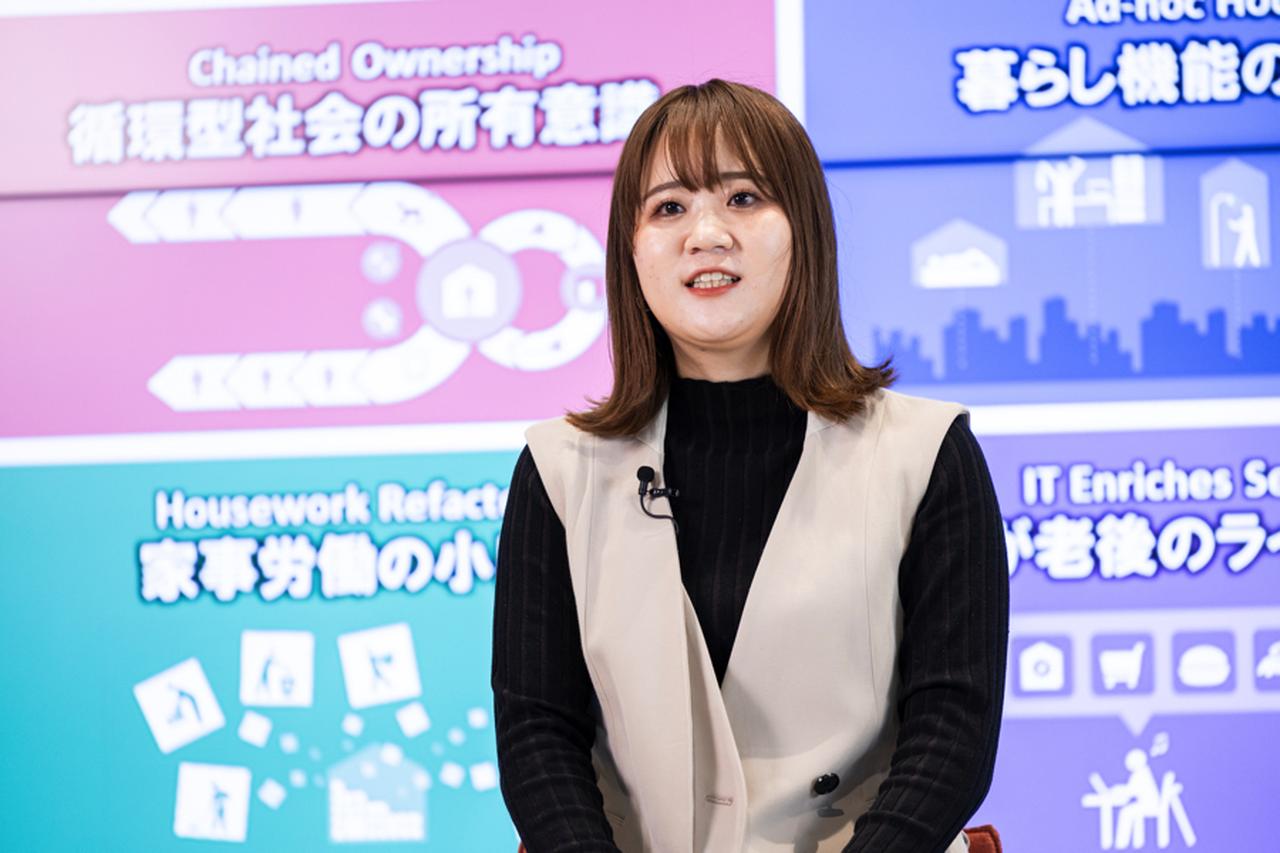
貝印の遠藤社長へのインタビューで印象的だったことをシェアする木田
木田:
Commitment for Disposingについて貝印株式会社の遠藤社長にお話を伺いました。人々の生活に身近な日用品のメーカーで、30年も前から失敗を恐れずに積極的に環境負荷の低い製品開発に注力されている企業です。
企業として多様化する価値観に寄り添える選択肢を用意することを大事にし、製品ラインアップとして、従来のもの、環境に配慮したもの、コスト重視のものをそれぞれ用意するなど、生活者の価値観の多様性を尊重したモノ作りをされています。
生活者に環境貢献を無理強いするのではなく、選択肢を用意した上で、それぞれがそれぞれのタイミングで地球環境に配慮したいと思ったときに製品を選ぶ、その日々の積み重ねを大切にしていけば、社会は徐々に変化して環境に配慮した製品を選ぶことが当たり前になるはずだ、と遠藤社長がおっしゃっていたことがとても印象的で素敵だと思いました。
同じモノ作りをしている企業として、日立も生活者の新しい価値観を後押しするきっかけを作りたいと思っています。
助口:
生活者の価値観はどんどん変わってきていると思いますが、皆さんは実際の暮らしの中で今までと違う価値観でモノを選んだり、サービスを使ったりという経験はありますか。
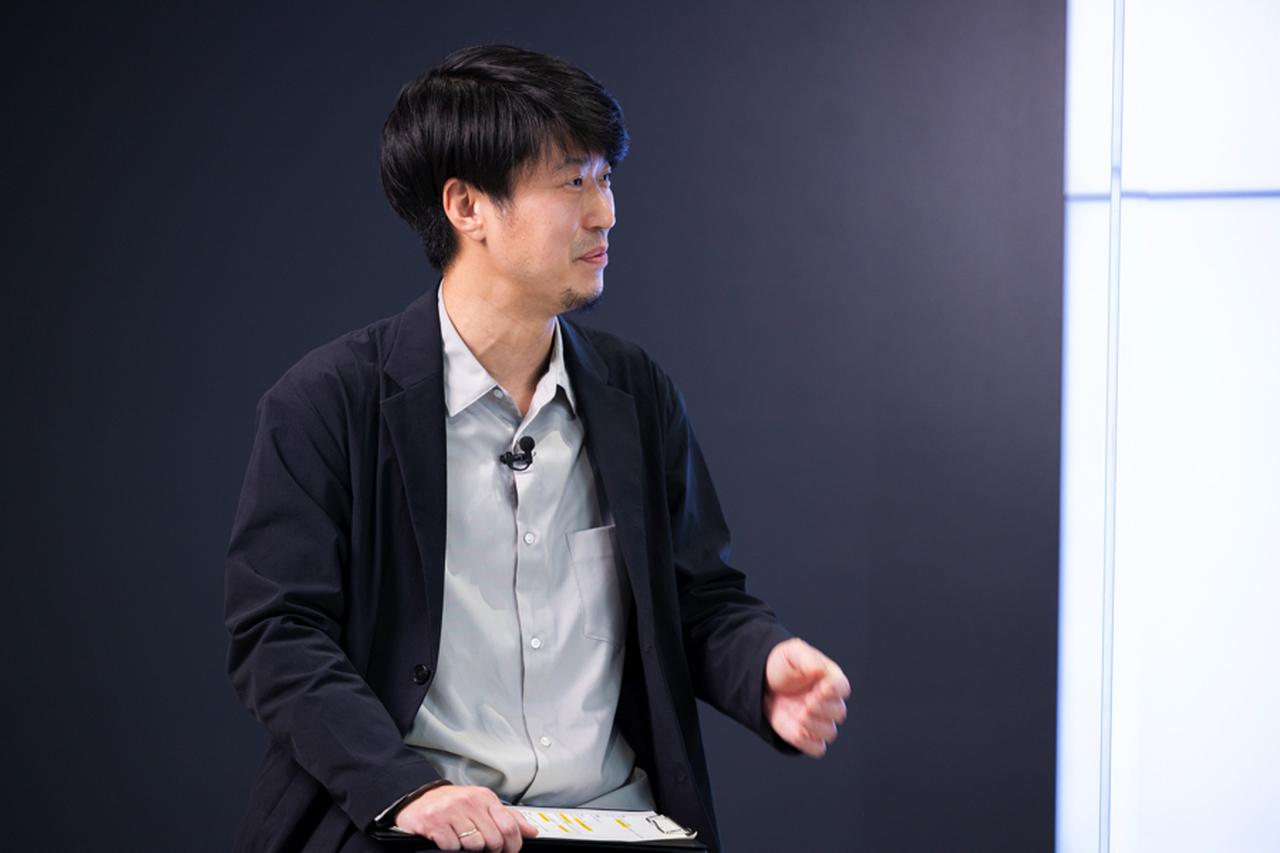
司会進行を務めた助口
八木:
私は雨が降っていた時に傘を借りられるアプリを使ったことがあります。その場しのぎで傘を買うより便利だなと思いつつ、先ほどのCommitment for Disposing、シェアリングすることで廃棄を減らすという新たな意味に気づくことができました。最近は、役に立つことはもちろん、これまで気づかなかった新しい意味を付加してくれる製品やサービスが増えてきていると実感しています。
栗城:
先日、再生材を使用したスニーカーを買いました。デザインだけでは一つに決めきれませんでしたが、その中の一つに「再生材を使用しています」という表記があり、思わず「これいいな」と買ってしまいました。環境配慮をしている製品かどうかが、社会でモノを購入する際の決め手の一つになってきていますね。
掃除機の外観に再生材を使った日立のチャレンジ
助口:
生活者の環境意識の変化やモノを選ぶときの視点の変化を受け、日立のモノ作りや野村さんが担当されているデザイン開発もずいぶんスコープが変わってきているのではと思います。
野村:
デザインという視点で生活環境の意識の変化を捉えつつ、環境対応の製品にどのような表現が求められるかを常に考えています。再生プラスチックを掃除機に使おうとしたとき、バージン材よりも異物が混入しやすく色ぶれが出やすい材料をどう使うか考えました。
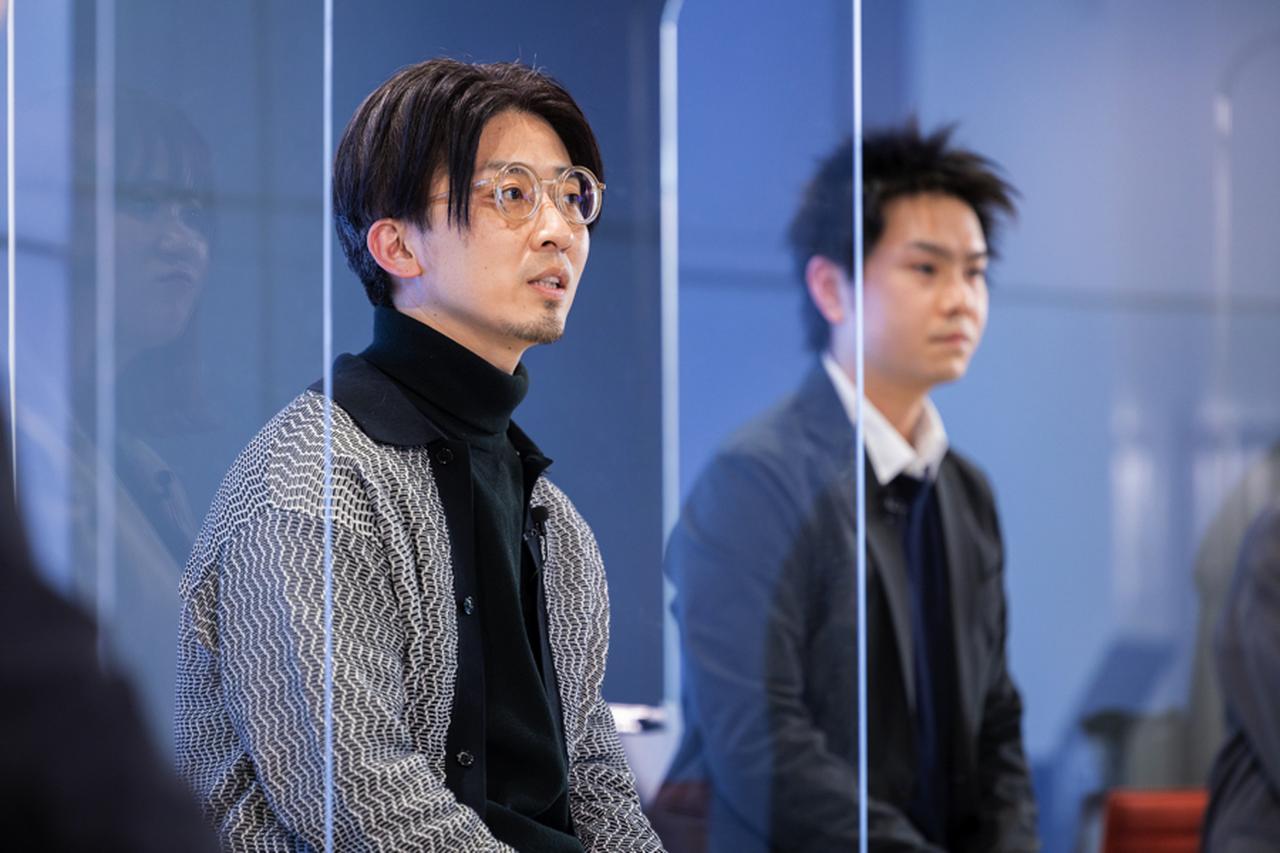
デザインの立場として、再生プラスチックを掃除機の外観に使おうと考えた経緯を語る野村
研究当初は、家電の外観に再生プラスチックが使われているものはまだまだ少なかったので、どのような表現が適しているかについて、ファッションやインテリアなどの業界からさまざまな分析を始めました。
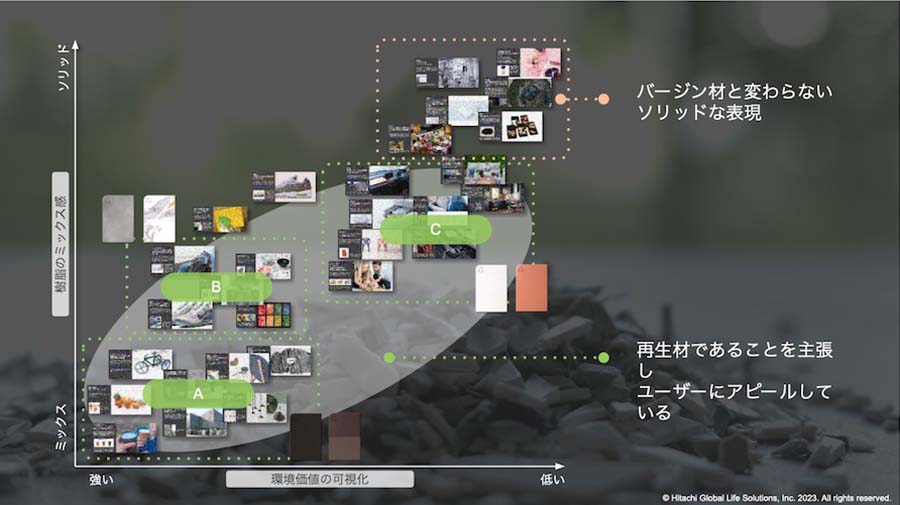
ファッションやインテリア業界では、再生材の使用をどう表現しているか
このマッピングからも分かるように、多くの企業が外観の素材に混ぜ物をして、再生材を使用していることをあえて分かるようにしています。これは、会社やユーザーが環境貢献していることを可視化するようなデザインが求められていたからではと考えています。
そこで私たちも、環境価値を可視化するような表現を施しながら再生材活用の課題を解決できるデザインを提案しました。
助口:
今画面に出ているのが、初期のデザインですね。
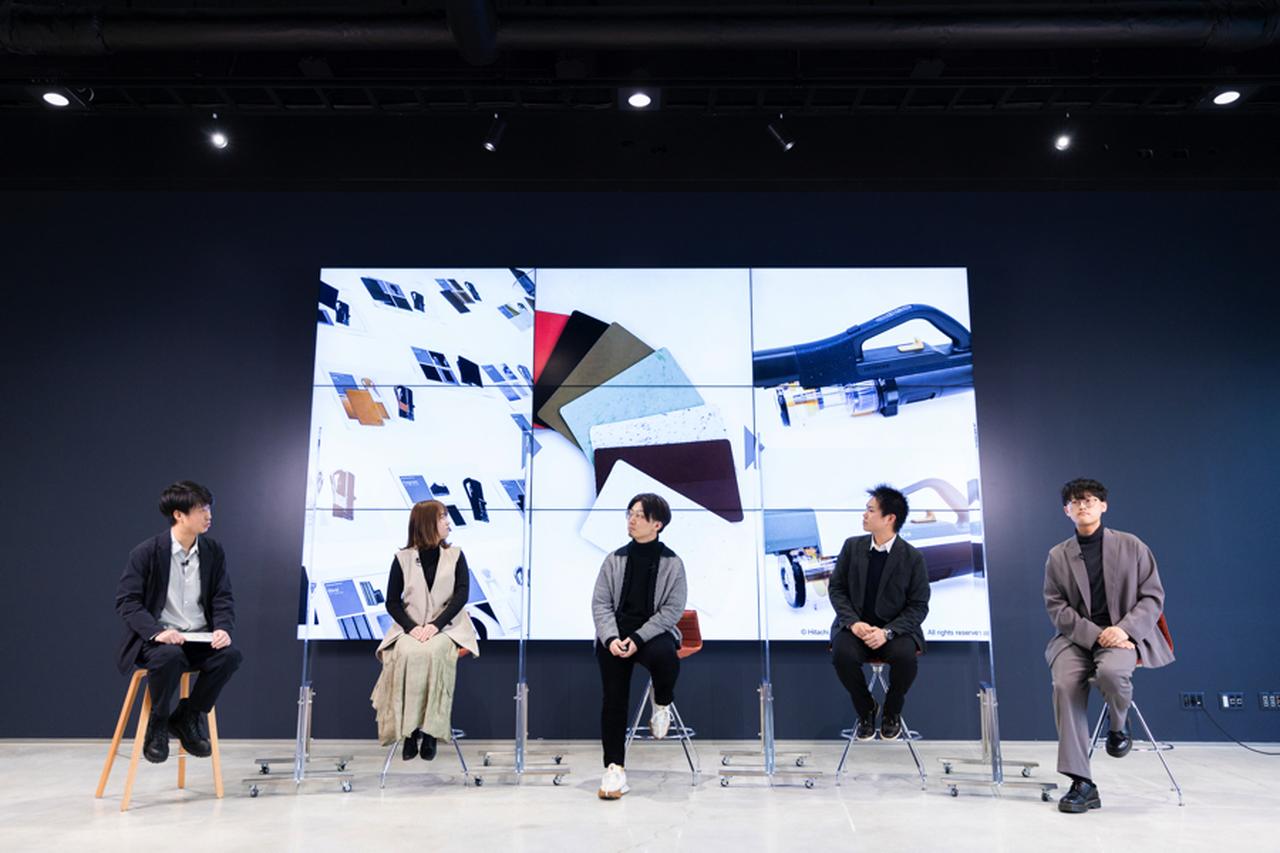
背景画像の一番右が、掃除機の初期のデザイン
助口:
栗城さんはこういった提案を最初デザイナーから受け取った際、技術、製造の立場としてどう感じましたか。
栗城:
設計としてはこれまでも内部部品のような目立たないところへ再生材を適用していましたが、今回外観部品へ適用したいと聞き、ぜひ積極的にチャレンジしたいと思いました。
一方で、再生材を使うためには解決すべき課題も多く、難易度が高いとも感じました。再生材はバージン材と比べて、特性がどうしても不安定になりやすい傾向があるからです。意図的に混ぜ物をすると意匠性はすごく良くなりますが、その反面、試作品では混ぜ物と再生材との密着性の部分で特性の低下が見られてしまいました。また混ぜ物をした場合、その製品を廃棄し、さらに部品を再利用することを考えると、果たしてサーキュラーエコノミーに適しているのだろうか、とも感じました。
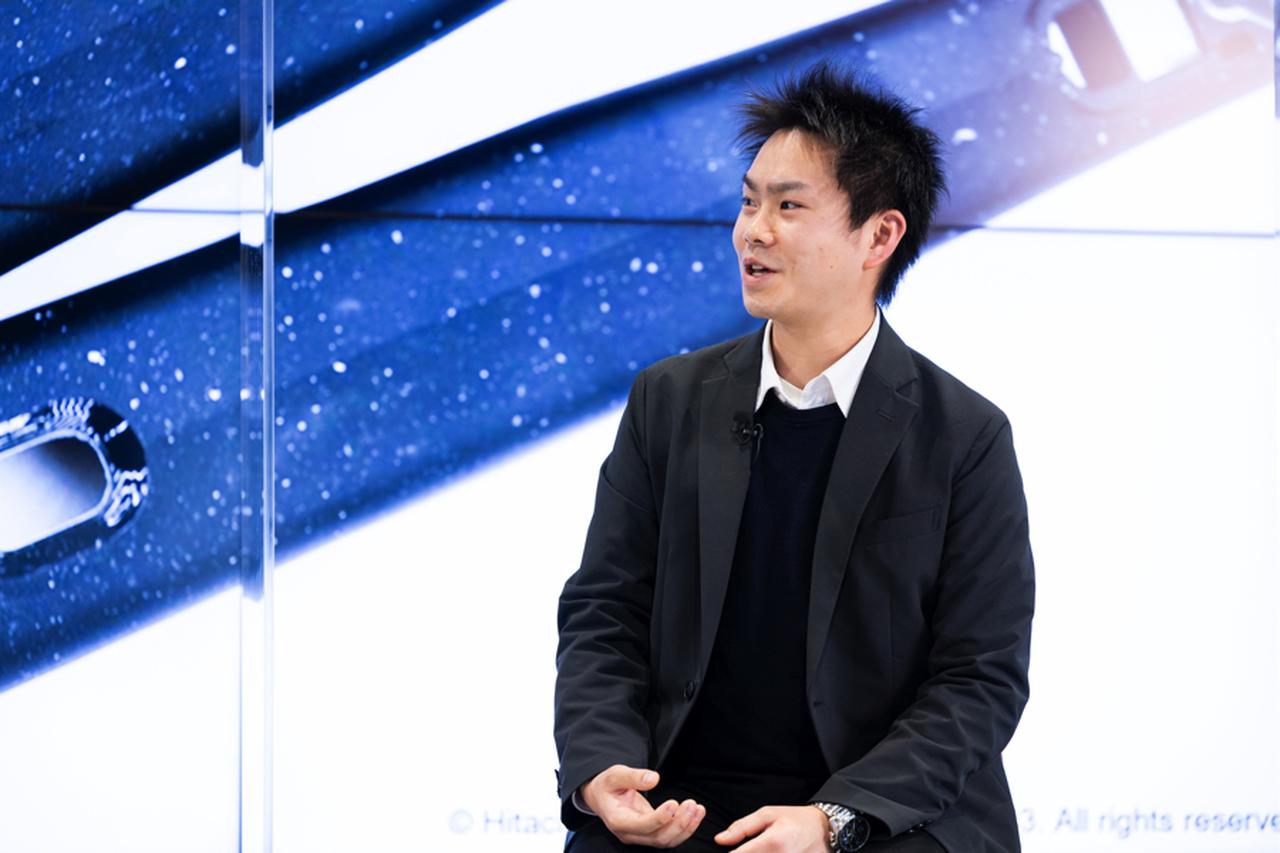
再生材を使う際、設計の立場で見えてきた課題について語る栗城
助口:
設計部門からのフィードバックを受けてデザインも見直しが必要になりましたね。
野村:
栗城さんの検討結果を踏まえ、私たちも考え方を大きく変えることにしました。ユーザーが再生材を受け入れ、再生材が当たり前になる社会が来た時に、再生材らしい表現だけではなく、再生プラスチックでバージン材とほぼ遜色のない意匠性を担保できるという認識を再構築できないかと考えました。
最初に、再生プラスチックに入った異物を目立たないようにするために、製品全体をダークトーンで構成するということから始めました。そして一色だけではモノトーンになり、製品がのっぺりとして魅力的ではないものになるので、ある程度コントラストをつけられないかと考えました。
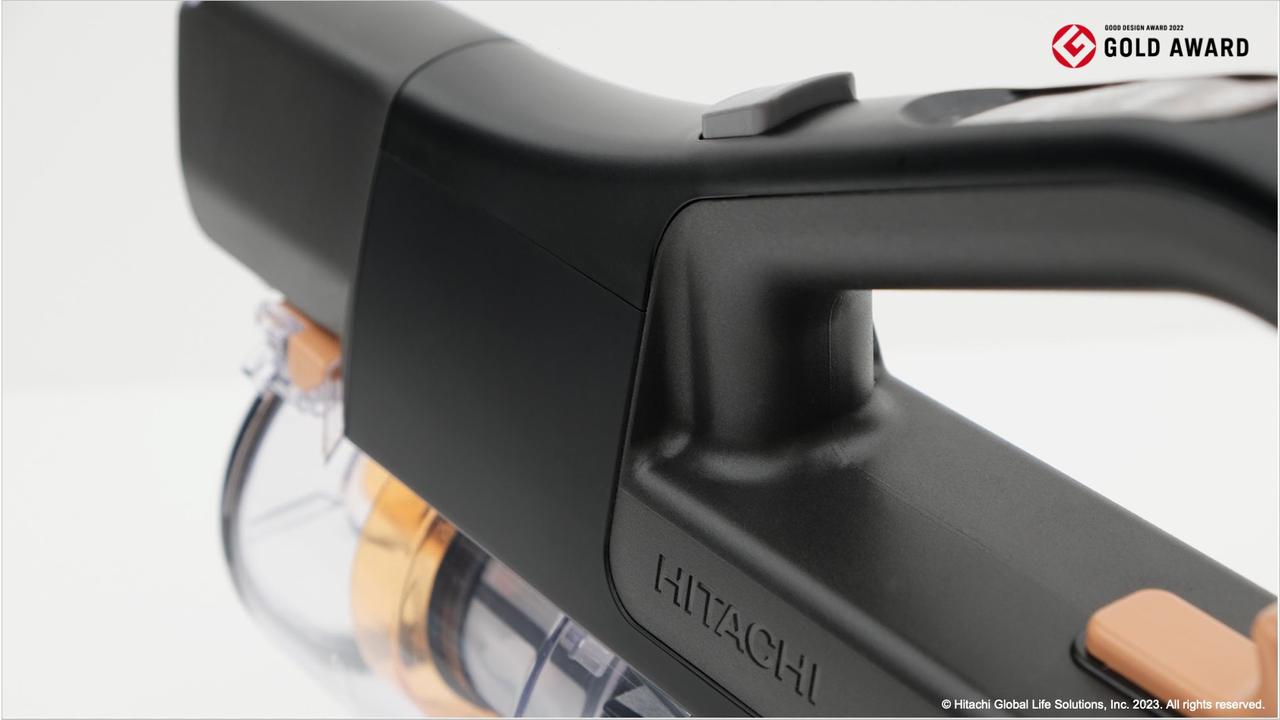
再生材を使い、深い黒色のコントラストでデザイン性を高めた掃除機
この写真は既にコントラストが出ている状態です。この写真にあるような深みのある黒を再現できないかというところで、今回素材も見直すことにしました。
ここで重要となったのが再生ポリカーボネートという素材です。一般的な再生プラスチックは既に着色されたプラスチックを使うことになるため、黒く染めても真っ黒になりません。そこで、透明素材として比較的入手しやすい再生ポリカーボネートを使うことで、黒く染まりやすい深い黒が再現できるのではないか、と提案しました。
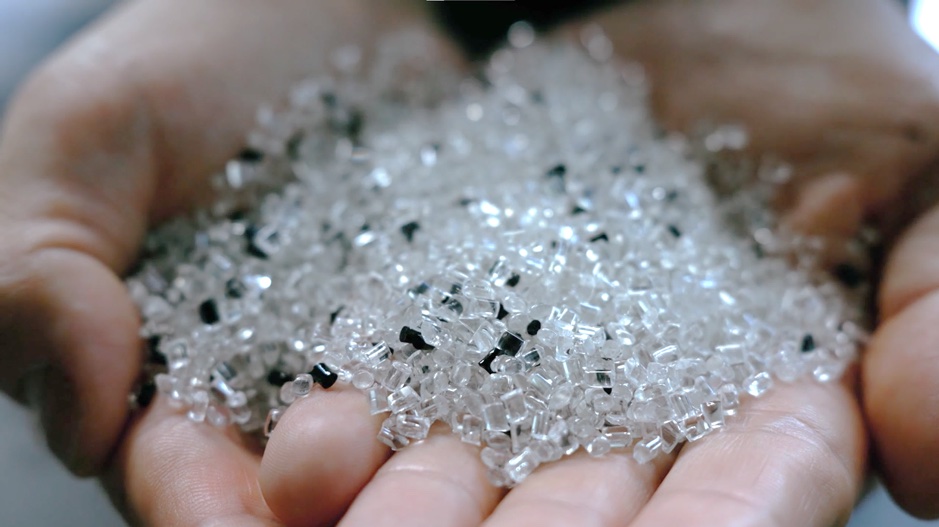
デザイン性の高い掃除機を実現するカギとなった再生ポリカーボネート
助口:
再生材を使った深い黒の印象はいかがですか。
木田:
とても格好いいと思いました。デザイン自体が格好いい上に知らず知らずのうちに環境に配慮できる製品であれば、私自身も使ってみたいと思いますし、友人にも薦めて、無理なく環境に配慮できるような製品がもっと広まってくれたらなと思いました。
AIを使った技術で再生材を安定して使いこなす
助口:
量産に向けてはまだまだハードルがあると聞いています。
栗城:
野村さんからお話があった通り、再生材は生産ロットによって色のばらつきが生じてしまうことが課題の一つだと私たちも考えていました。その点、今回透明の材料を使ったことは再生材を適用する上で重要なプロセスの一つだったと考えています。使用する再生材が決まった後に苦労したのが意匠面の仕上げです。
再生プラスチックを使用する部品にはシボという仕上がりを変える表面処理を施しています。再生材はロットによってばらつきが出やすいので、さまざまなロットを使っても仕上がりが安定する成形条件を見つけることにとても苦労し、時間を要しました。この経験から、再生材の適用をより拡大していく上では、ロットごとの違いを補正するような技術の確立が今後必要だと感じています。
助口:
このあたりの非常に難しい課題に技術的に取り組んでいるのが八木さんです。八木さんの研究をお聞かせください。
八木:
再生材の適用を拡大する上で、三つの課題があると私は考えています。一つ目は、再生材はバージン材と比べて材料の特性が低下する場合が多いこと。二つ目は、栗城さん、野村さんの先ほどのコメントにもありましたが、劣化や異物混入によって外観品質にばらつきが生じてしまうことです。三つ目は材料の特性がばらつくことで成形品の品質もばらついてしまうことです。
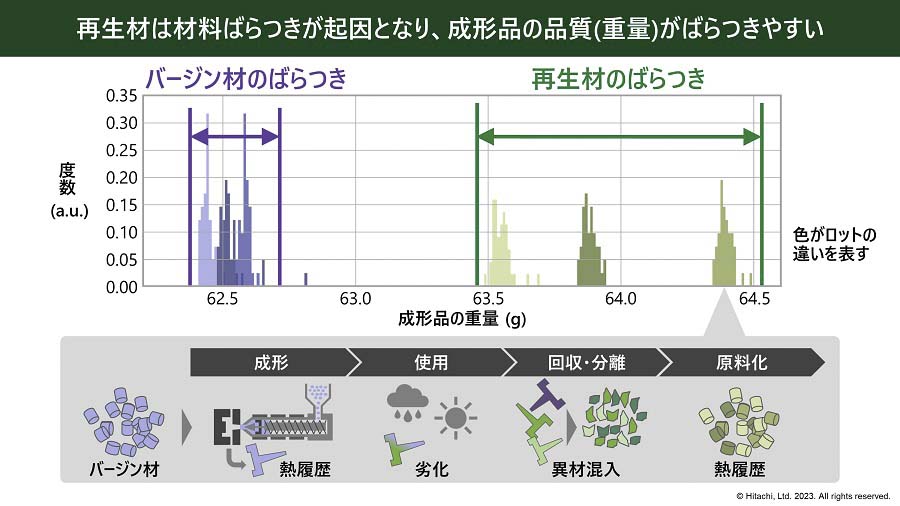
バージン材を使った場合と、再生材を使った場合との成形品の品質ばらつきの違い
八木:
リサイクルの過程で、材料特性が多様になることで、結果として成形品の重量など、機械的特性のばらつきが大きくなる場合があります。スライドでは、紫色がバージン材の成形品の重量、緑色が再生材の成形品の重量を示しています。色の違いがロットの違いを示していますが、ロットが変わると、再生材の成形品の品質は大きく変化する場合があります。
栗城:
確かに再生材の特性が変わってしまうとその変化に合わせて成形条件などを都度見直す必要があり、量産ではやはり製造現場の負担になるケースが出てきてしまいます。また、ロットの違いによる成形品の品質を補正する方法が、製造現場の方のスキルに依存してしまうのも課題の一つかなと思います。
八木:
そこで私は再生材を製造現場の方のスキルによらずに使いこなすためのAIを開発しています。プラスチックを成形する射出成形※というプロセスにおいて、材料ロットごとに材料特性が変動することを逆手に捉えて、材料特性に応じた成形プロセス条件、例えるなら成形品を作るためのレシピを生成します。
開発技術には、量産前に実施する学習モードと量産中に実施する逆解析モードの二つのモードがあります。学習モードでは材料特性が変動している再生材を、センサーを搭載した金型を用いて成形し、その特性をセンシングし、特徴量を抽出します。データベースにセンサー特徴量などを溜め込むことで、成形プロセスの条件、再生材のセンサーの特徴量、成形品の品質が紐づいたデータベースを作ります。
※射出成形…金型を用いた成形法の一つ。主にプラスチック(合成樹脂)を加熱して溶かし、金型に射出して成形する。
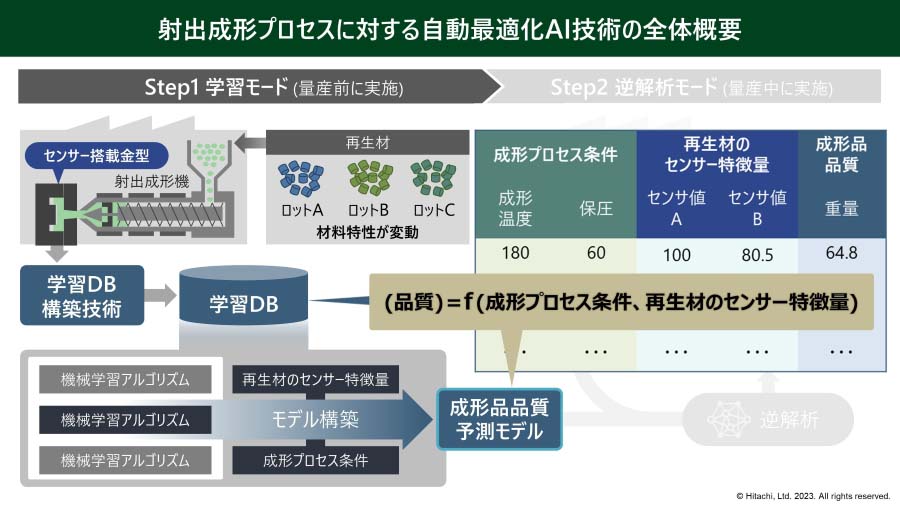
量産前に実施する学習モードの概要
助口:
ちょっと難しくなってきましたが、実際に特性がばらついている再生材を成形してみて、その仕上がった成形品の重量を計測して、それをデータベースに蓄積していくという理解でいいですか。
八木:
その通りです。そして、このフィジカルなデータを活用して、再生材のセンサーの特徴量と成形プロセス条件から、成形品の品質を予測するモデルを、機械学習の技術を使って構築します。
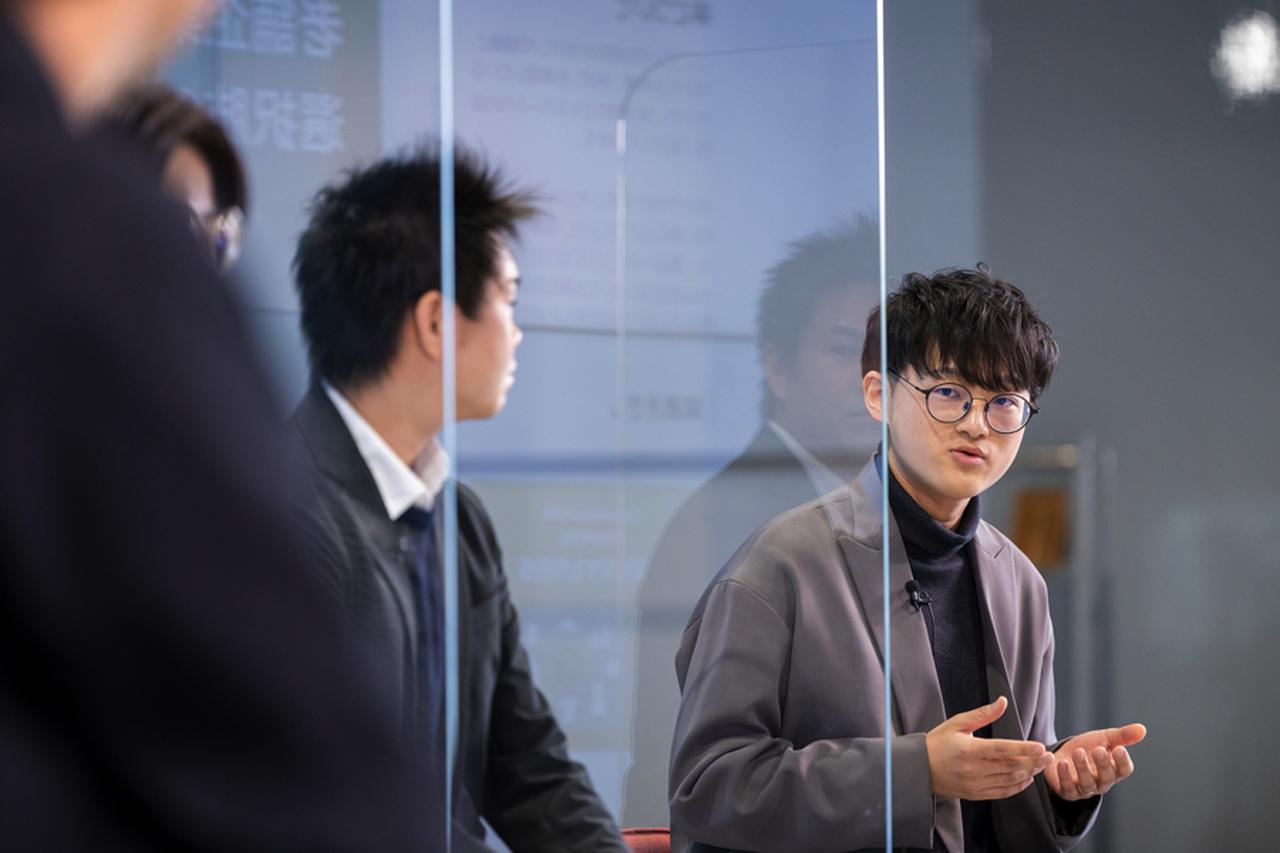
AI技術を活用した品質予測モデルについて説明する八木
助口:
この予測モデルを構築するのにAIを活用しているということですね。
八木:
はい。実測データを学習して、プロセス条件と材料を指定するとどれぐらいの品質になるかを予測するAIですが、実はこのAIにどういう形で学習させるかが非常に重要で、そこにAIはもちろん、射出成形のナレッジが詰め込まれています。
栗城:
そのようなフィジカルとデジタルが融合できるノウハウを持っているのは日立の強みの一つかなと思います。
八木:
量産時は逆解析モードということで、まず最適化する再生材のロットに対して、センサーを搭載した金型のセンシングデータから特徴量を抽出します。そして、先ほど求めた成形品の品質予測モデルに目標値となる品質の値とセンサー特徴量を入れると、モデルの中の三つの変数のうち二つが埋まるので、逆解析という手法を使って成形プロセス条件を求めることができます。そしてこの最適化するロットに適したプロセス条件を制御に反映することで品質を安定化させます。
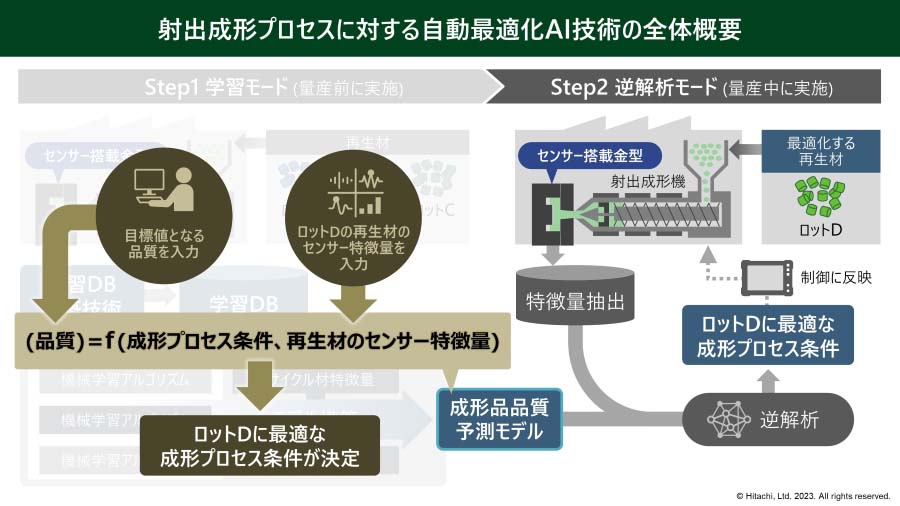
量産中に実施する逆解析モードの概要
実際に、この技術を複数のロットに適用した例です。
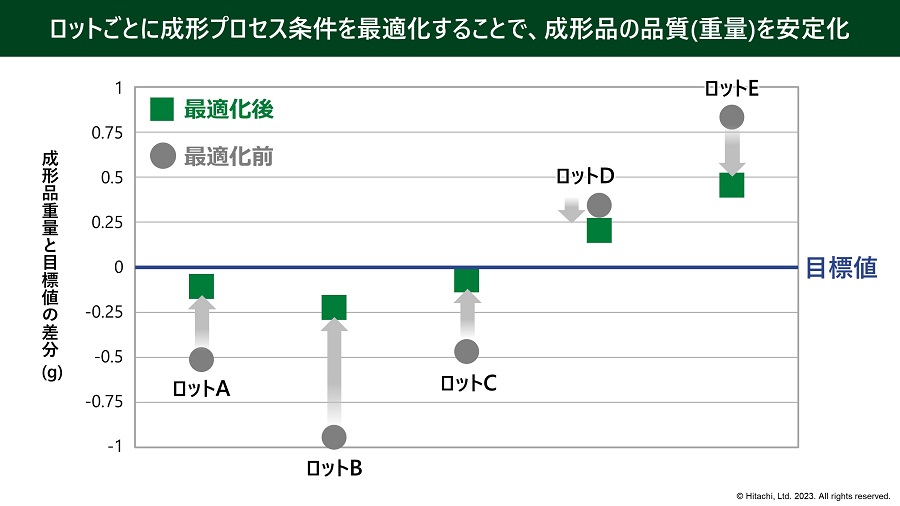
AI技術を活用したことによって品質が安定化した
縦軸が品質を表す成形品の重量、横軸がロット、グレーの丸が最適化前、グリーンの四角が最適化後のロットです。このようにロットごとに成形条件を個別最適化することで、各ロットの成形品の重量がターゲットにした目標値に近づき、全体として品質が安定化します。
野村:
デザインの視点からもばらつきのある材料を使いこなせるようになれば、使用できる材料の幅が広がるのですごく助かります。
八木:
この技術は、製造面だけではなくデザインの可能性を広げることや、調達の安定性、レジリエンスの向上にも有効な技術ではないかと私は捉えています。プログラム2でもサーキュラーエコノミー実現に向けて、デジタルトランスフォーメーションが重要だという議論がありましたが、この取り組みもその一つの事例になると思っています。
助口:
最後に皆さんが今後チャレンジしていきたいこと、取り組んでいきたいことについてお話しください。
木田:
私は今までは社内向けの発信やインナーブランディングが中心でしたが、これからは社外にも、日立は技術を駆使して生活者の将来の価値観変化に寄り添った商品開発をしているということをもっともっと発信してアピールしていきたいと思っています。
野村:
今回取り組んだ掃除機については、あくまで再生プラスチックを活用できた一つの事例だと考えています。今後も各製品に適した再生材の使いこなしを研究し、製品への適用を加速していきたいと考えています。
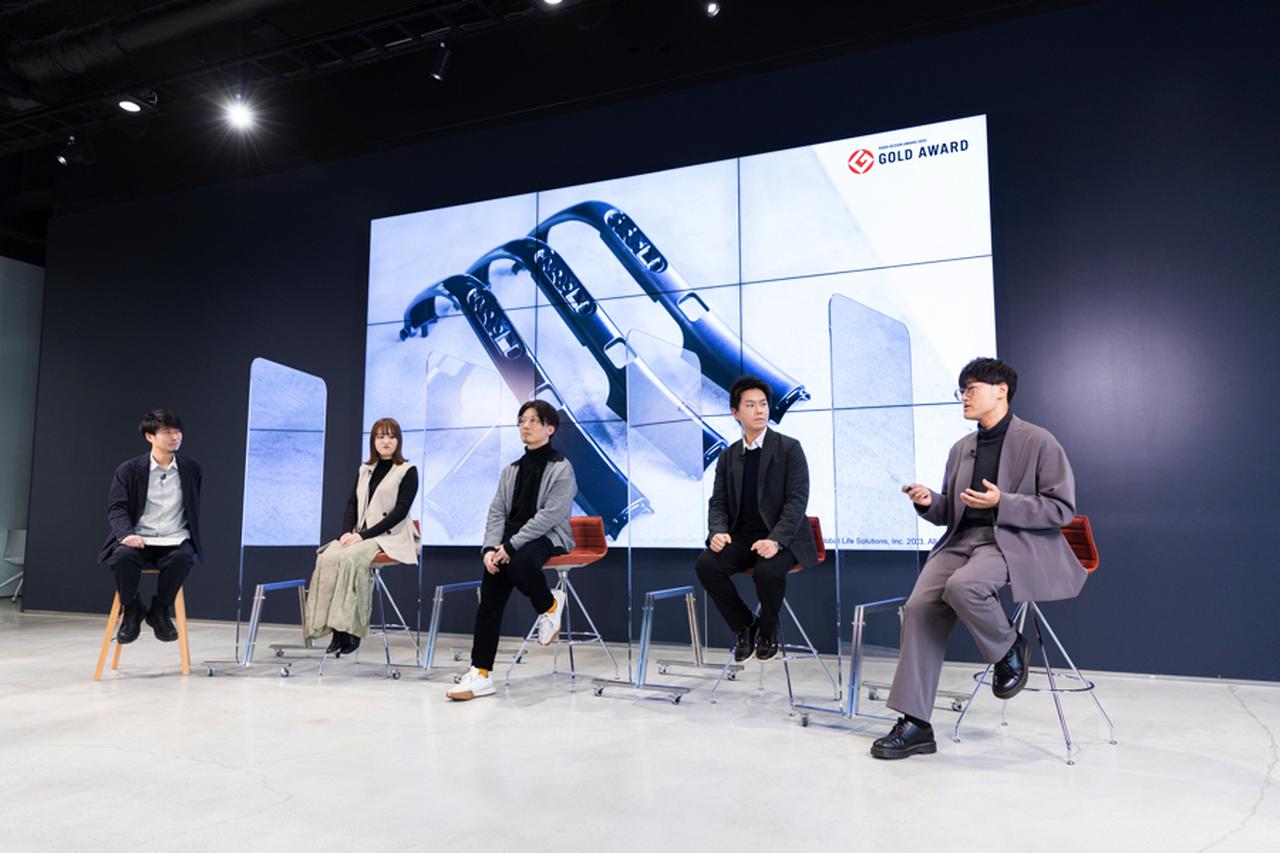
企画、デザイン、設計、研究者が一つになって製品開発を進めていこうと想いを新たにした5名の登壇者
栗城:
これからもこういった取り組みは加速していくと思いますので、今回せっかくつながることができた皆さんと二人三脚で取り組んでいきたいと考えています。
八木:
私は木田さんの説明にあった、貝印の遠藤社長の「価値観を無理強いするのではなくて多様な選択肢をユーザーに提供する」ということが自分にとっていい気づきであり、とても共感しました。多様な価値観に寄り添う上で、どういう技術が必要か、今回ご紹介した技術を深めながら、この問いに対する一つのアイデア、選択肢を提供できる研究に取り組みたいと思っています。
助口:
日立は今後も、生活者の皆さんの価値観変化に応えられるような製品サービス開発を企画、デザイン、設計、研究者一丸となって進めていきたいと思っています。
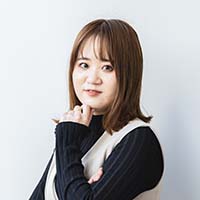
木田 萌未
日立グローバルライフソリューションズ株式会社 ビジョン戦略本部 ビジョン商品企画部 主任
2013年日立アプライアンス株式会社(現日立グローバルライフソリューションズ株式会社)に入社後、調達本部にて白物家電の部品調達やサステナブル調達の推進を担当。
2022年より現職にて中長期ブランディングに従事。

栗城 潤也
日立グローバルライフソリューションズ株式会社 生活家電本部 第二設計部
2018年日立アプライアンス株式会社(現日立グローバルライフソリューションズ株式会社)に入社後、国内向け充電式掃除機の設計に従事。2022年に再生プラスチックを活用した掃除機の設計を担当。
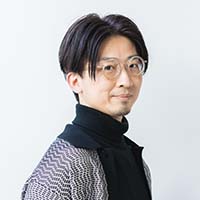
野村 皓太郎
日立製作所研究開発グループ デザインセンタ UXデザイン部 主任デザイナー
2004年日立製作所入社、携帯電話、白物家電などのプロダクトデザインを担当。現在は冷蔵庫を中心に家電のデザイン開発を担当しつつCMFのタスクフォースチームなども取り纏めている。
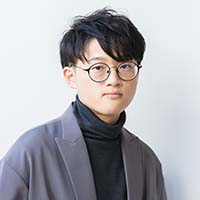
八木 大介
日立製作所研究開発グループ 生産・モノづくりイノベーションセンタ サーキュラーインダストリー研究部 研究員
2018年日立製作所に入社後、機械学習の応用をはじめとした製造プロセスのデータ活用に関する研究開発に従事。化成品、金属素材、パワー半導体など幅広い製造現場のDXに携わり、2020年からは再生材の使いこなしなど、環境×デジタルを実現する技術開発を推進。
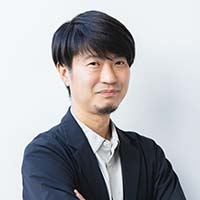
助口聡
日立製作所研究開発グループ デザインセンタ UXデザイン部 部長
日立グループが手掛ける製品、サービスのデザイン開発を取りまとめるプロダクトデザイナー。2018年までは英国に駐在し、高速鉄道車両のコンセプトデザイン開発にも従事。
プログラム1「サーキュラーエコノミーの現状と日立の取り組み」
プログラム2「サーキュラーエコノミーがめざす社会と経済」
プログラム3 パネルディスカッション「サステナブルな製品開発への挑戦」